PRODUCTS
Loomis Products provides the following products to our customers
WET BAG ISOSTATIC PRESS
Isostatic pressing is the high-pressure shaping of powdered materials (powdered ceramics, refractories, clays, metals and plastics) into various shapes and sizes. LOOMIS PRODUCTS offers both Wet Bag and Dry Bag Isostatic Presses in a variety of sizes and pressure ratings.
Working Pressure up to 100,000 psi
Automatic pressing cycle
Carousel Tool Indexing – Fill, Press, Unload, and Tool change/clean
Parts production per customer specification.
Typical cycle times 3 – 20 min (depending on press size & part)
PLC control – Push button / Visual Touchscreen / PC Inputs
Hydraulic closure manipulation
Digital pressure read-out with hi/lo contact
LOOMIS PRODUCTS Automatic air vent valve
LOOMIS PRODUCTS Pilot operated check valve for pre-fill/suction
LOOMIS PRODUCTS special decompression valve
Air over oil intensifier
Electric / Hydraulic Intensifier
Clean/Dirty pressing fluid filtration
Ease of operation & maintenance

DRY BAG ISOSTATIC PRESS
Isostatic pressing is the high-pressure shaping of powdered materials (powdered ceramics, refractories, clays, metals, and plastics) into various shapes and sizes. LOOMIS PRODUCTS offers both Wet Bag and Dry Bag Isostatic Presses in a variety of sizes and pressure ratings.
Working Pressure up to 60,000 psi
Automatic pressing cycle
1 to 4 pressure vessels
Carousel Tool Indexing – Fill, Press, Unload, and Tool change/cleaning
Parts production per customer specifications
Typical cycle times 30 - 120 sec (depending on press size)
PLC control – Push button / Visual Touchscreen / PC Inputs
Hydraulic operation – long service life of pumps and valves
Digital pressure read-out with hi/lo contact
Pilot operated check valve for pre-fill/suction
LOOMIS PRODUCTS special decompression valve
High-pressure intensifier
Ease of operation & maintenance
Auxiliary equipment

PISTON/RAM EXTRUDER
LOOMIS PRODUCTS piston extrusion presses are used to process powdered ceramics, metals, and plastics into a wide variety of profiles ranging from simple cylinders and tubes to complex honeycomb shapes. With capacities exceeding 800 tons, our piston extrusion presses are available in 9 standard configurations and are capable of producing parts per customers specifications.
-
Standard configurations: 5 - 800 Tons
-
Special Applications up to 1200 tons
-
Parts production: size/shape per customer specification
-
Double Tilt System variable extrusion & fill angle 0 - 90° (View Animation) "Patent 3,898,831"
-
Side Swing System "Patent Pending"
-
Tilt / Side Swing System" Patent Pending"
-
Accurate control of extrusion speed and pressure
-
PLC control – Push button / Visual Touchscreen / PC Inputs
-
Simple Tool changeout
-
Ease of operation and maintenance
-
Minimal wear of Material Cylinder & Pressing Ram
-
Cutting / Unloading systems
-
Loading systems

CONTINUOUS EXTRUDER
Applications up to 500 tons
Accurate control of extrusion speed and pressure
PLC control - Push button / Visual Touchscreen / PC Inputs
Simple tool changeout
Ease of operation and maintenance
Minimal wear of material cylinder & pressing ram
Horizontal, Vertical or Inclined

CLOSED-LOOP SPEED CONTROL
The Loomis Closed-Loop Process Control system is an extremely precise method for maintaining extrusion speed, which results in a more uniform density in green parts. This precise control is possible by using the latest motion control and linear positioning technology combined with servo- positioning and velocity control devices. At the heart of the Loomis closed-loop extrusion control system is the closed-loop hydraulic module; a multi-axis closed-loop process controller with process times below 2 milliseconds per loop cycle. The Loomis Closed Loop Process controller can make adjustments in milliseconds rather than tenths of seconds (or even seconds) which is often the case with an open or single loop controller. The result is a process that can quickly reach and maintain the velocity set point. Motion control modules are connected directly to the PLC (programmable logic controller) I/O Bus, allowing commands to be executed almost instantaneously. This is in contrast to external closed-loop systems in which the commands must negotiate communications protocols before sending executable commands to the controller. In addition to the benefits of sharing a bus, instructions and parameters can be incorporated into the PLC Logic Program which allows for smoother and more complete system integration.
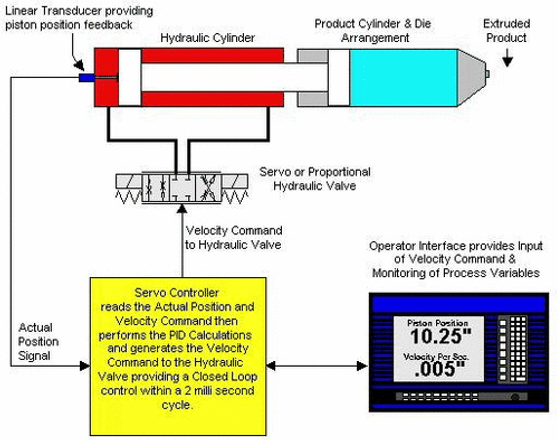
ISOSTATIC LABORATORY PRESS
Wet Bag or Dry Bag configurations
Custom sizes available
Variable pressure build-up
Adjustable dwell time
Closure lift and guide system
2 circuit hydraulic system oil/water
Top closure manipulator

LABORATORY EXTRUDER
-
Compact 16 or 25 Ton Design
-
Accurate control of extrusion speed and pressure
-
PLC control - Push button / Visual Touchscreen / PC Inputs
-
Simple tool change out
-
Ease of operation and maintenance
-
Minimal wear of material cylinder & pressing ram
-
Horizontal, Vertical or Inclined

HIGH PRESSURE COMPONENTS
The use of custom-designed high-pressure components such as Decompression valves, One-Shot Intensifiers, Pilot Operated Check Valves, Inline Check Valves, and High-Pressure Relief Valves are essentially what sets us apart from our competition.
These high-quality components are now available on a ' build on-demand ' basis and can be built to customer specifications.
Decompression Valves - Hydraulic and Pneumatic
Decompression valves control the rate at which the pressure of the compressed fluid is released, which in turn reduces flow surges in high-pressure systems. Excess flow is metered to a tank, in response to an electrical or pressure signal to the valve control.
Metering the excess flow to the tank before shifting the directional control valve also reduces system decompression vibration and noise.
LOOMIS PRODUCTS offers Hydraulic and Pneumatic Decompression valves in a wide range of sizes and pressure ratings.

ONE SHOT INTENSIFIERS
Pressure intensifiers are used to increase the pressure of hydraulic fluids in pressurized systems. Intensifiers use a large quantity of low-pressure fluid to produce a smaller quantity of higher-pressure fluid. LOOMIS PRODUCTS offers Intensifiers in a wide range of sizes and pressure ratings.

PILOT OPERATED CHECK VALVES
Pilot-operated check valves are used to positively hold a pressurized load and then release the load upon application of a pressure signal to the pilot port. Pilot-operated check valves help prevent cylinder drift and provide protection against load loss in the event of hose or tube failure. LOOMIS PRODUCTS offers Pilot operated valves in a wide range of flow and pressure capabilities.

CUTTING SYSTEM
LOOMIS PRODUCTS has been designing and building Cutting and Handling Systems for almost as long as it has been designing and building Isostatic presses and Extruders.
​
​While most systems have been built to Customer specifications, LOOMIS PRODUCTS offers 'stand alone' designs that can be fitted directly to existing machines that are already installed in the field.

SPARE PARTS
LOOMIS PRODUCTS includes a Spare Parts List as part of the Operators Manual that is provided with every machine we build. Our recommended Spare Parts List covers critical components that we believe should be kept on hand (at the Customer’s facility) to service equipment quicker and minimize downtime. While LOOMIS PRODUCTS does inventory many common parts, it is imperative that Customers follow the recommendations contained within the manual. Spare parts available from LOOMIS PRODUCTS include high-pressure components, hydraulic fittings, hoses, and electrical controls...as well as replacement Polyurethane Tooling.
